By Dewayne Imsand
J.W. McCoy produced the first known onyx pieces in 1910. The pieces he made were a ardinière, a matching pedestal, and an umbrella stand as shown to the left and in the center below. All of these pieces were offered in both a “Red Onyx”, which was actually a reddish dark brown color, and in a blended glaze.
In 1911, the name of the J.W. Pottery Co. was changed to the Brush-McCoy Pottery Co. and in that year a newly designed jardinière and pedestal was introduced in Red Onyx. The jardinière and pedestal is shown on the right above.
During 1914, the jardinière and pedestal sets shown above, along with other pieces were offered in both a Red or Green onyx.
In 1924, the Brush-McCoy pottery introduced a large number of onyx pieces that the company referred to as our “New Onyx Line.” The new line came in an assortment of shapes as shown on the catalog page below. An example of the 1924 Brush-McCoy onyx is shown to the left.
In early 1925 the Brush-McCoy pottery came out with a new onyx piece.
This time the piece was a pitcher. In addition, the pitcher introduced two new glaze colors, Blue Onyx and Brown Onyx. Also in 1925 the company produced a large selection, about 40 pieces of onyx ware, and each of these pieces was available in either, Red, Blue, or Green.
The Flower Bowl and candlesticks shown on the front cover are examples of this 1925 onyx.
The Flower Bowl came in two sizes, an eight and nine-inch diameter. The bowls also came with a black base, which was probably made of ebony. The candlesticks that were made in 1925 had a ring handle. The candlesticks without handles, as shown, were identical to the 1925 candlesticks but were made sometime later. Other pieces from a 1925 catalog are shown on page 13. Another page from the 1925 catalog is given on the rear cover.
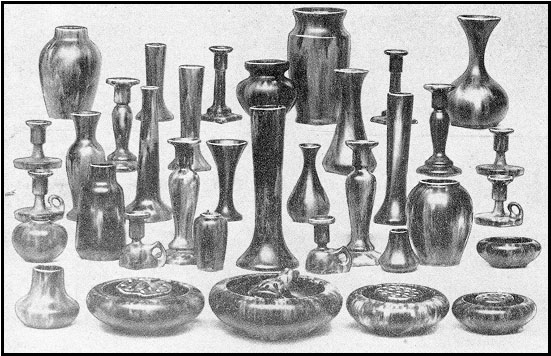
A 1924 Brush-McCoy Catalog Page
At this point I would like to offer a little discussion of onyx. All of the pieces that are called onyx are not the same type onyx. Also, sometimes there is confusion in determining if a particular piece is onyx or if it has a blended glaze. Both the onyx ware and pieces with a blended glaze are created using a procedure called over-glazing. In this process, a second color, or sometimes a third color glaze, is applied to an initially glazed piece. Although in both of the two types of over-glazing the glazes blend together, a difference occurs because of the manner in which the second and any subsequent glaze is applied.
In creating blended ware an additional color or colors may be applied by using a brush, or more typically, if one color is added, by dipping the top of the piece in the additional glaze. Subsequently, when the piece is up-righted and fired all added glazes run down the sides of the ware for varying distances and the colors tend to blend in streaks.
In the early onyx pieces the secondary color or colors are stippled all over the ware. Stippling is a method of applying color by daubing the tip of a brush loaded with a colored glaze at intervals all around the sides of the ware. This produces a pattern, shown to the right below, that is sometimes more noticeable than at other times.
The major difference seen between blended ware and the earlier onyx ware is that in onyx ware the secondary color or colors are renewed at spots all over the sides of the ware so that the over-glaze or glazes are not confined to streaks. Since both blended ware and onyx ware are glazed by hand, each piece is unique and there are many variations of each style of them.
In December 1925 the name of the pottery was changed from the Brush-McCoy Pottery to the Brush Pottery. Four years later, in 1929, the company came out with another onyx line. It was called “Modern Blended Onyx”, and the glaze was applied to the company’s Stonecraft Line, which had first been introduced in 1923. It is not known whether this new “Modern Blended Onyx” was applied to any other pieces or not, but a Stonecraft jardinière with the new glaze is shown to the left. While the upper portion of the jardinière has a solid color glaze, the lower sides which is the onyx portion, are clearly typical of the blended glaze technique.
Although this new line, Modern Blended Onyx, was solely a Brush Pottery Co. product, the date it came out, 1929, is important because it marks the time that a noticeable difference between the original type onyx and a newer type appeared.
The question may be asked, “Why was there a change in the way onyx pieces were made?” The most probably reason for the change began years before. In 1921, the U.S. War Department conducted an investigation to determine which minerals had been in short supply during World War I. The list of minerals included tin, which was an important ingredient contained in onyx glazes. This metal, together with lead caused the original onyx glaze to be heavy and thick, and to have deep and very rich colors. In addition, their use created an excellent blending of the different colored glazes to occur. Although the U.S. Government did not begin a program to stockpile the minerals that were identified earlier until 1939, the minerals undoubtedly were scarce and expensive years before then.
It appears that due to the scarcity of tin, and its expense, a substitute formula for the onyx was developed. Lead used by itself results in a clear glaze that shows colors well and has depth, but tin was needed to make the old onyx. When lead is combined with tin oxide in proportions of about one part lead to three parts tin, the glaze takes on the onyx characteristics. In the new formula it is not certain if the use of lead was discontinued at this time, but titanium dioxide was substituted for the more scarce tin oxide. The result of the change was a thinner glaze and one which did not produce the deep rich colors and the superb blending as before. For example, the earlier reddish, dark brown that was called “Red Onyx” was now a lighter brown.
There is another difference too. Typically on the older onyx pieces the glaze blending goes down the sides of the piece to the very bottom. The secondary glaze, or glazes, on the latest onyx pieces stops short and does not extend to the bottom. To the left above is an example of a latter day Brush-McCoy piece, and in the center and to the right are two examples of latter day Nelson McCoy pieces. I will discuss more about the Nelson McCoy pottery onyx pieces below.
Since some of the glaze would run off the piece in the older type onyx, it could cause a sticking problem within the kiln when the piece was fired. To remedy this problem additional manufacturing steps had to be adopted.
In order to eliminate sticking to the kiln plate, or sagger (a large ceramic box that holds the pieces as they are being fired), each piece was placed on a pontil. A pontil is simply a small devise consisting of a base with three small, pointed vertical stilts that are positioned in a triangular shape. These stilts raise the piece above the plate or sagger floor so any excess glaze can drip off and permit the piece to be removed after firing without it sticking.
The use of a pontil causes the base of the pieces to be irregular due to the varying amount of fired glaze clinging around the edge of the base. Therefore, the base of each piece was placed on a grinding wheel and smoothed so that the piece would sit upright. The grinding creates an unglazed ring, or sometimes a partially unglazed ring, around the perimeter of the base.
Additionally, since the points of the stilts are surrounded by glaze when the piece they support is fired, each stilt leaves a small spot on the bottom when the stilt is removed from the piece. These marks which resemble little popped blisters are called pontil marks. In the photo to left may be seen the three evenly spaced marks around the inside perimeter.
In the early 1930’s, after the onyx glaze formula was changed the severity of the sticking problem was decreased, since the secondary glaze(s) did flow all of the way to and off the bottom of the pieces.
This allowed the use of the pontil to be discontinued. Care was still necessary however, to prohibit the primary glaze from sticking, but alternative methods were available.
One method was to scrape the glaze off the bottom of each piece before firing, but a faster and better way was soon adopted. This method involved the use of hot wax. According to Nelson McCoy, this method was used by his pottery, and it is assumed that it was used by the Brush-McCoy pottery too.
In this method, each dipper or glaze person had a hot plate and skillet that contained a piece of carpet that had a certain knap and thickness, and lots of wax. The dipper would lower each bisque piece into the wax soaked carpet to a depth just enough to coat the very bottom of each piece. On pieces that had a bottom with a concave center surrounded by a raised outer ring, the wax would just be applied to the outer ring. On other flat-bottom pieces, the wax would cover the entire bottom. After the wax was applied the piece was fired. During the firing the wax eliminated any sticking and it would burn away leaving no trace.
It was necessary that the dipper kept the wax at a certain height in the hot skillet, because if too little wax was applied to the foot, the piece would catch glaze and stick, and if there was too much wax, the piece would have a bare place on the side where there was no glaze.
Besides the lack of pontil marks on the newer type onyx, there is one other difference between the older and newer onyx pieces. The older pieces were made using a yellowish, colored clay, whereas the newer pieces were made using a white or cream-colored clay.
As time went on the Brush pottery continued making onyx pieces throughout the years of its existence, but as mentioned above, the J.W. McCoy, Brush-McCoy, and the Brush potteries were not the only makers of onyx ware. After the name of the Nelson McCoy Sanitary Stoneware Co. was changed in 1933 to the Nelson McCoy Pottery Co., they also produced an onyx line.
It is believed that the onyx formula Nelson McCoy first used was the thick glaze formula that had the rich coloring, just as the J.W. McCoy and Brush-McCoy potteries used. A 1933 Nelson McCoy catalog page showing the shape of the pieces the pottery initially made is given on page 14. Information does not exist to showing a subsequent grouping of Nelson McCoy onyx pieces. However, a number of individual pieces, mainly jardinières and vases, are known to have been produced.
Compared to solid colored pottery, or pottery with blended colors, the production of onyx, as has been shown, is a more labor-intensive operation. For this reason, or a decreased demand, or some other cause, the Nelson McCoy pottery only made onyx pieces for a few years, probably less than three or four. After that time, the production of blended glazes became the multi-glaze method of choice. Along with this glazing style and the use of solid colored glazes, in both bright and matte shades, the Nelson McCoy pottery produced many other innovative glazing styles throughout the life of the pottery.